What is An Induction Motor?
What does electromagnetic induction depend on and how does it relate to single phase AC motors?
An induction motor is an AC electric motor in which the electric current in the rotor needed to produce torque is obtained by electromagnetic induction from the magnetic field of the stator winding. The rotor can be either wound type or woundless, permanent magnet type.
What is Electromagnetic Induction?
Electromagnetic induction is the process by which an electromotive force is generated in an electrical conductor by a changing magnetic field. It is one of the fundamental principles of electricity and magnetism and is the basis for many applications such as electric generators, motors and inductive heating.
The magnetic field can be generated by either a moving magnet or a changing electric current. When the magnetic field changes, it induces an electric current in the conductor.
You can read more about AC motors here: AC Motors: How Do They Work?
How Induction Motors Work
The operation of an induction motor is based on the interaction between a rotating magnetic field (RMF) and an electro-magnetically induced field in the stator winding to produce torque on the rotor.
When the stator windings are connected to an AC power supply, a rotating magnetic field is set up in them. The magnitude and direction of this RMF is dependent upon the phase angle of the applied voltages with respect to each other.
If a three-phase supply is used, then the resultant RMF will rotate at a constant speed known as synchronous speed.
Speed control of induction motors can be achieved by varied techniques like changing the slip, varying the applied frequency or using rotor resistance control etc.
Single-phase induction motors are used extensively for numerous domestic applications such as:
- air conditioners
- washing machines
- clothes dryers
- refrigerators
- pumps
- fans
Parts and Construction
Single Phase Induction Motors have several key components that work together to produce rotational force. These components include:
Stator: This is the stationary part of the motor that contains the windings and generates the magnetic field.
Rotor: The rotor is the rotating part of the motor and contains the conductor that is subjected to the magnetic field generated by the stator.
Shaft: The shaft connects the rotor to the load that the motor is driving.
Bearings: The bearings support the shaft and allow it to rotate smoothly.
Frame: The frame provides support for the other components and protects the motor from external forces.
Winding: The winding is the conductor that is wrapped around the stator and carries the current that produces the magnetic field.
Starting Methods
There are several starting methods for single phase induction motors, including:
Split Phase Starting Method: This method uses two separate windings, a main winding and an auxiliary winding, to generate a magnetic field.
Permanent Split Capacitor (PSC) Starting Method: This method uses a capacitor to provide the necessary starting torque. The capacitor is connected in series with the auxiliary winding and is disconnected once the motor reaches its operating speed.
Capacitor Start Induction Run (CSIR) Starting Method: This method uses a capacitor to provide starting torque and to improve the performance of the motor during operation. The capacitor is connected in series with the auxiliary winding and remains connected during operation.
Capacitor Start Induction Motors (CSIM)
Capacitor Start Induction Motors use a capacitor to provide the necessary starting torque. The capacitor is connected in series with the auxiliary winding and is disconnected once the motor reaches its operating speed.
The working principle of a capacitor start induction motor is based on the interaction between the magnetic fields generated by the stator windings and the rotor conductors. The capacitor provides the necessary starting torque by producing a leading current in the auxiliary winding that interacts with the magnetic field generated by the main winding.
The advantages of capacitor start induction motors include improved starting torque, reduced current surge during starting, and improved performance at high speeds. However, they are not as efficient as other types of motors and are more expensive to manufacture.
Capacitor Run Induction Motors (CRIM)
Capacitor Run Induction Motors use a capacitor to provide both starting torque and improved performance during operation. The capacitor is connected in series with the auxiliary winding and remains connected during operation.
The working principle of a capacitor run induction motor is based on the interaction between the magnetic fields generated by the stator windings and the rotor conductors. The capacitor provides a leading current in the auxiliary winding that interacts with the magnetic field generated by the main winding to produce a smoother, more efficient operation.
The advantages of capacitor run induction motors include improved efficiency, improved performance at high speeds, and reduced current surge during starting. However, they are not as efficient as other types of motors and are more expensive to manufacture.
Advantages vs Disadvantages
Advantages:
- One advantage that induction motors have over DC motors is that they are self-starting without any need for external starting devices like resistors or star-delta starters.
- Another advantage of induction motors over synchronous motors is that they do not require exact synchronism between rotor and stator speeds for producing rotating magnetic fields.
- One more advantage of induction motors over DC machines is that there are no sparks due to commutation thus avoiding fire hazards in many environments including chemically treated atmospheres like those found in textile and paper mills etc., where there may be explosive gases present.
Disadvantages:
- Disadvantages include lower power factor at low speed (especially for squirrel cage types), larger size for same power output when compared with synchronous motors (wound rotor has same size as synchronous machine), lower efficiency at part loads (due to ohmic copper losses) and more maintenance (brushes).
- Starting torque also tends to be low especially for squirrel cage types although this can be improved somewhat by adding resistance to the rotor circuit (wound rotor).
- Another disadvantages common to all AC machines relative to DC machines is that high inrush currents occur during start-up; this requires large fuses or contactors capable of withstanding these high currents which may cause reliability problems in some cases if they are not specified correctly.
- Low power factors also result in poor voltage regulation thereby requiring larger transformers than would otherwise be necessary if power factors were higher.
This increases overall system cost and complexity since it means that larger capacity cables will also be required resulting sometimes in difficulties ensuring suitable copper or aluminum conductor sizes are available especially where multiple feeders exist from one substation feeding different parts of an industrial complex for example.
Finally, caution must ALWAYS be exercised during maintenance operations on AC equipment since contact with ‘live’ conductors may result in severe injury or even electrocution.
Personal protective equipment such as insulated gloves and tools must always be used when working on such equipment!
In general, AC equipment is more expensive than equivalent DC types primarily due to the increased complexity associated with rectifier circuits etc., but this disadvantage may be offset somewhat by their longer life expectancy due their inherently rugged construction and simple maintenance requirements relative to DC types.
AC gearless traction motors used on many modern rail locomotives provide an excellent example where reliability requirements demand a design life expectancy of 30 years with minimum maintenance thereby providing considerable economic advantages over earlier DC designs despite their increased initial capital cost which was rapidly offset by savings achieved through reduced running costs and maintenance requirements together with improved availability compared with DC designs.
Exploded View
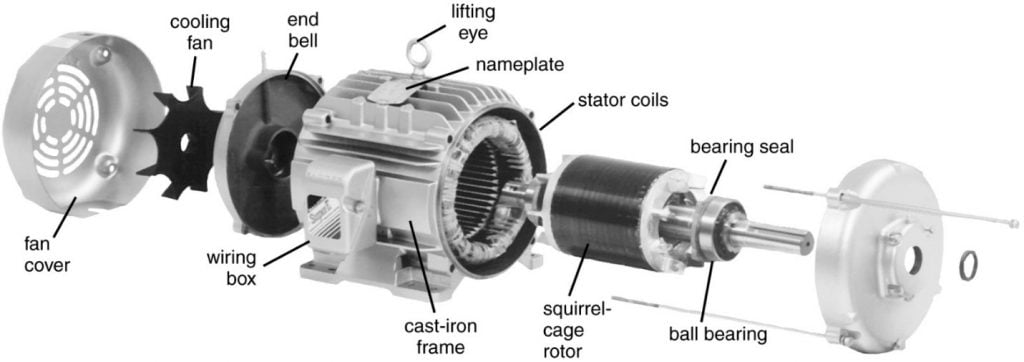
Useful Resources
AC Induction Motors: A Workhorse for Any Job
Induction Motor Fault Diagnosis
FAQ
What is another name for single phase induction motor?
Single phase induction motors are sometimes referred to as asynchronous motors.
What is the main advantage of using an induction motor?
The main advantage of using an induction motor is its simplicity, reliability, and cost-effectiveness. Induction motors are also known for their durability and long lifespan.
Why are single phase induction motors used?
Single phase induction motors are used in a variety of applications due to their simplicity and affordability. They are commonly found in household appliances, such as refrigerators, air conditioners, and washing machines.
Can a single phase motor run without a capacitor?
Yes, a single phase motor can run without a capacitor, but its performance will be reduced. A capacitor is often used in single phase induction motors to improve performance, including starting torque and efficiency at high speeds.
Are single phase induction motors AC or DC?
Single phase induction motors are AC motors. They use alternating current to produce a magnetic field and generate torque.